David French is the country managing Director of JS International Inc., a construction firm that makes pre-fabricated houses, with a factory in the Kigali Special Economic Zone (KSEZ) at Ndera, Gasabo District.
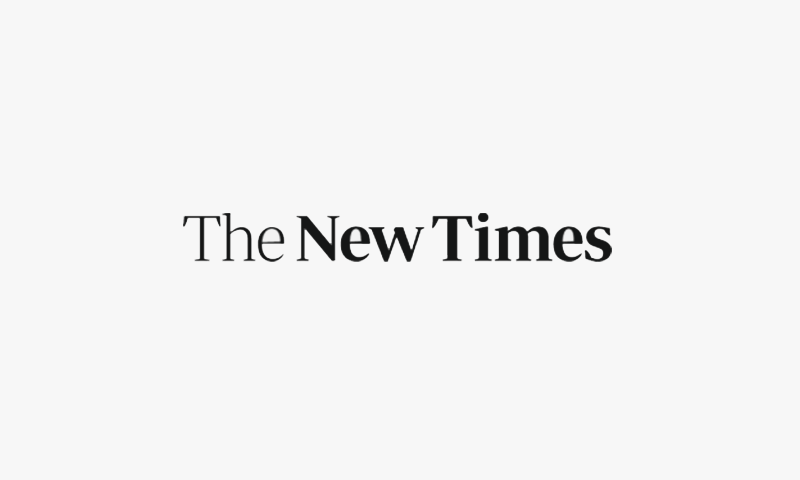
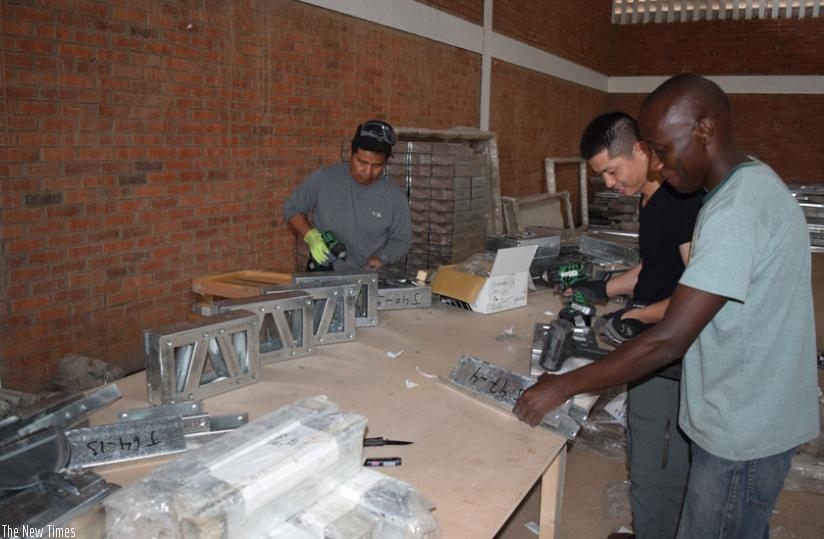
David French is the country managing Director of JS International Inc., a construction firm that makes pre-fabricated houses, with a factory in the Kigali Special Economic Zone (KSEZ) at Ndera, Gasabo District. The company has already embarked on various real estate projects in Kigali that will be ready in the coming months. French briefed Business Times Stephen Kalimba about the project, the firm’s internship programme and its plans:
The government is encouraging real estate investors to build affordable homes for citizens. Where do you fit in?
The way we approach it is different from some companies, but the intention is to help Rwanda address the housing issue…We are targeting people like police officers, and other government workers, as well as corporates in steady jobs. But we also build for the high-end market.
Whatever the target market, we do not compromise on quality. If we are building houses for middle-income earners or building a five star hotel, the quality is same. We use the same high quality steel and other components; everything is the same, except the finishing, the tiles and cabinets.
I prefer to call them entry-level houses because when you say affordable, who are you talking about? When you say low-income earners, people find that offensive. That’s why we prefer to call the houses entry-level homes.
What is your target market?
We would like to do a lot of entry level housing (affordable homes)…it’s better to serve a big market than a small one (high-end). Many companies look at the mid-level market, where the money is, but our approach is different because we want every Rwandan to have a decent modern home.
Besides, we want to establish Rwanda as our East Africa hub, from where we will spread to the rest of Africa. So we have to first meet the country’s housing needs, as well as those of greater East Africa region since it has one of the biggest housing requirements in the world.
We discussed with the Rwanda Social Security Board (RSSB) to see how we can work together to provide affordable houses. RSSB recently said they have affordable housing projects where homes go for about Rwf13 million to Rwf30 million. So, we want them to us the opportunity, give us a price bracket so we set our version of an entry-level house. These figures could seem high but they are realistic. However, we can also build you units worth $10,000 (Rwf7.5 million) but these could be for the upper lower end of the market pyramid.
However, the bottom line is for sector stakeholders, including government, to work together and find innovative ways to provide citizens affordable homes.
You have an extensive plan for the entry level housing, what’s your motivation?
I have been in construction for most part of my life. When I was a school-going child, I used to watch my elder brothers build houses.
Later after school, I joined them…We worked for many years in the war zones in Iraq and Afghanistan, providing affordable houses using this technology (pre-fabricated steel).
What materials do you source locally?
There’s a company called SH Industries that produces stone chip roofing which is of nice quality. There are two or three other companies we have spoken to, like Master Steel, for possible partnerships.
Though we are not necessarily going to tie ourselves to one company, we want to use roofing materials that are made in Rwanda. We don’t need to import anything if it is made here. We want to support local firms.
We are going to work with Papyrus to supply us with kitchens, cabinets, windows and doors for the houses. We want to source those on the local market. Our system is environmental-friendly, encouraging solid wood doors is not good because we are cutting down the rain forests to produce them.
So, we want to use hollow section doors and particle boards made of recycled wood. It’s an environmental-friendly door. However, we use wood for the main entrance doors.
We will work with Papyrus and equip them with skills to produce particle doors.
For steel, we source from the region for a company that can produce the high quality products we need. Our target is anything between 1,000 and 10,000 tonnes of steel. This is cheaper and will eliminate a lot of the carbon effect, resulting from shipping them from the UAE.
Any challenges, especially as far as getting skilled personnel is concerned?
They may be few people with the kind of skills we want, but if you get ‘quick learners’ they will learn the will basics in a couple of weeks. We make sure they understand how connections work, for instance, and then send them to the site for hands-on practice in the actual erection of the houses.
What is your forecast for the next two, three years?
This year is busy one focusing a lot on the first phase projects. We are currently undertaking several projects, including one at Institute for War & Peace Reporting (IWPR), the Karumeyi Village Estate and Paj Real Estate, both in Kicukiro, and a maternity clinic for Dr Pierre Celestin Kanimba’s Polyclinique La Medicale in Kigali. Once these projects are completed in the couple of months or so, we will switch our attention to other projects. We anticipate a lot of interest once these projects are finished and are looking forward to more projects next year.
Do you have skills transfer programme to equip Rwandans?
We are presently trying to get an effective housing synopsis, but we have held talks with some people who have some training collaborations with local technical colleges where students come in for work-based training. We will adopt the same system. We are targeting students from universities and other tertiary institutions, studying engineering and architecture. Depending on their level, they will train with us for say two weeks, and then at the end get a certificate.
As a young and growing company, we want to employ many young people… those who have been on the training programme will automatically be taken on after their internship programme.
We are targeting four to six student interns at a time, but we will increase the number to 20 with time.
We will employ over 200 people, especially framers in the factory and at the different sites.
Kigali housing needs
The company has so far injected $2 million (about Rwf1.5 billion) into the project since it opened shop last year.
The firm produces some house components at its KSEZ plant.
The American company deals in general construction, with a particular interest in apartments, high-end housing and affordable homes. The challenge of lack of affordable housing, especially in urban centres like the City of Kigali, continues to trouble authorities. The situation is made worse by the fact that many real estate developers target the high-end market ignoring low-income earners.
It is estimated that presently the City of Kigali population growing each year, the city needs to build about 31,000 units annually, and 344,068 units will be required by 2020, according to research done by the city in 2012.
business@newtimes.co.rw