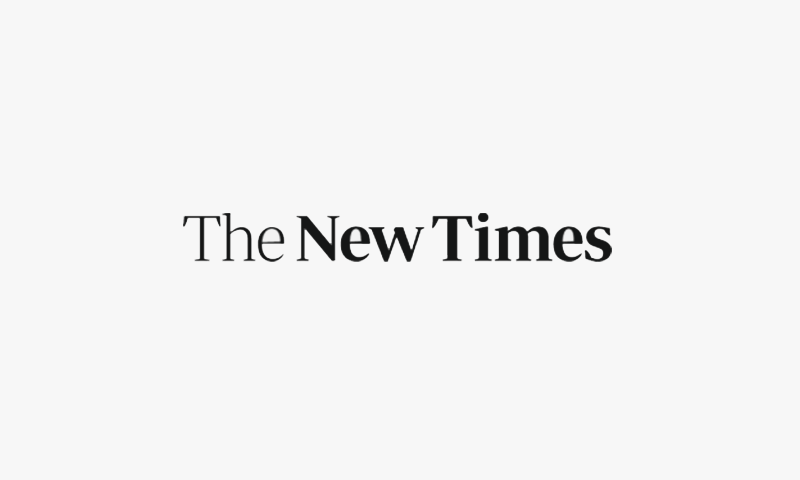
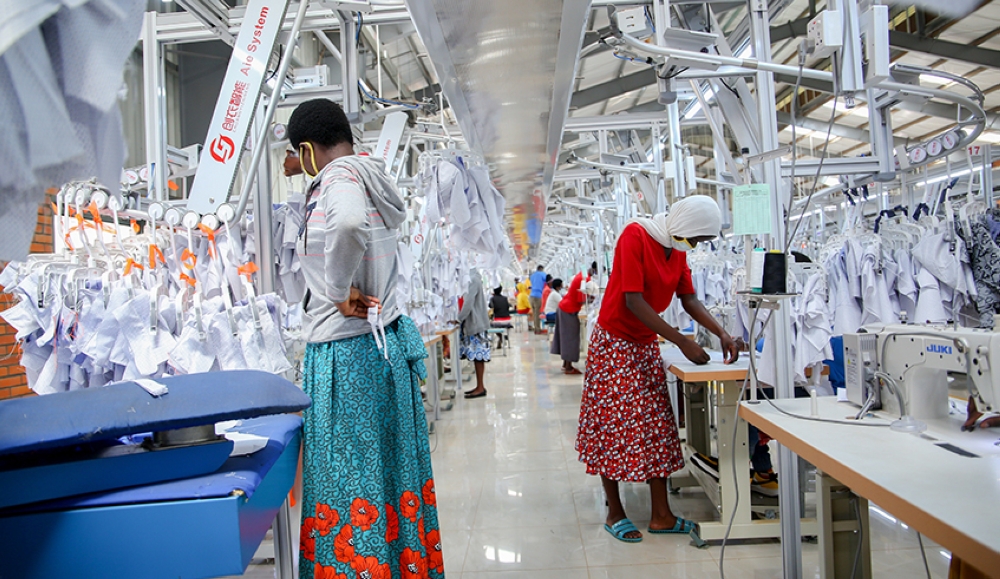
Players in the Made-in-Rwanda space are struggling under the weight of a myriad of challenges, including the high cost of raw materials, the ban on plastic packaging materials, competition from imported substitutes, and generally disinterested clients.
Locally made products, especially clothing, have a reputation of being relatively pricy - which manufactures attribute to several factors.
This, even as figures show that locally made products have made inroads in the export market in recent years.
Statistics from the Ministry of Trade and Industry (MINICOM) indicate that Rwanda exported $34.6 million worth of textile and garment products in 2020, up from $5.9 million in 2018.
However, locally made products seem to be struggling in Rwanda.
This is mostly down to pricing.
According to Brave Japhet Ndamukunda, the founder of La Lune, a fashion house known for making suits in Rebero, a Kigali city suburb, the cost of raw materials is the single most important factor behind relatively high prices for Made-in-Rwanda products.
ALSO READ: Made in Rwanda is the right strategy for industrialisation
"We import different fabrics from East African Community member countries, and artificial fabrics, primarily polyester, from South Africa, Taiwan, Korea, and Indonesia. If we were creating our own fabrics, prices could be lower.”
Ndamukunda said there are also some companies that create Made-in-Rwanda products from scratch, which explains the high expenses.
Prices aside, he noted, "we still need to improve our quality and creativity, to allow the locals to support our very own products.”
ALSO READ: What should be done to elevate the "Made in Rwanda” sector
According to Yannick Ishimwe, the founder of F&Y Ltd, a local fashion brand, the quality of some local products has pushed consumers to be dependent on Eastern and Western products, and "in the end, this has resulted in unemployment".
A survey conducted by the National Institute of Statistics of Rwanda (NISR) indicated the unemployment rate among the youth (16-30 years) increased by 31.4 per cent in three months only, where it reached 29.7 per cent in November 2022, up from 22.6 per cent in August 2022.
Nadine Kanyana, a fashion designer and the chief executive of House of Kanyana, explained that some lcoal fashion brands are forced to lower their prices as a way to retain customers. "This limits their margin.”
For Kanyana, lowering prices calls for cutting production costs without compromising the quality.
Felix Habimana, the Made-in-Rwanda Secretariat Programme Manager at MINICOM, admitted that manufacturing goods in Rwanda may involve higher production costs compared to countries with larger economies.
Factors such as limited infrastructure, access to raw materials, and higher labour costs can contribute to increased manufacturing expenses, which can be reflected in the final product prices, he noted.
"Our country’s domestic market size is relatively small compared to countries with larger populations and established industries,” Habimana said.
He added that there is limited demand which may result in reduced economies of scale, which constitutes a challenge for local manufacturers looking for cost efficiency. As a result, production volumes may be lower, leading to higher costs per unit.
"Our country relies on imports for certain raw materials, machinery involves, transportation costs, and currency fluctuations, all of which have an impact on the overall price of locally manufactured products.”
Habimana further explained that Made-in-Rwanda products often strive to meet international quality standards to compete in global markets. Ensuring compliance with these standards may require additional investments in equipment, testing facilities, and quality control measures, which can contribute to higher production costs.
Yet, developing and upgrading skills and adopting advanced technologies can be costly for local manufacturers, he noted.
He said investing in training programmes, research and development, and technology acquisition can add to the overall expenses, which may be reflected in the prices of Made-in-Rwanda products.
Habimana explained that establishing effective marketing channels and distribution networks for locally produced goods can be a significant challenge, stressing that investing in marketing, branding, packaging, and expanding distribution networks can add to the overall costs, which may be passed on to consumers.
Meanwhile, some local industry players have cited packaging as a major challenge as the existing ban on plastic bags makes it difficult to find affordable alternative packaging, thus issues around handling. This has raised questions around pakaging quality to the extent it has discouraged potential buyers or driven away existing clients, sources said.
During an interview with The New Times, a well-known Made-in-Rwanda apparel manufacturer in Kigali who asked for anonymity, expressed concerns about the packaging problem. This issue, she said, hinders the ability of locally made clothes to compete with imported garments.
The clothing entrepreneur, who has been in business for five years and employs 246 workers, also pointed out that imported clothing, such as those from China, are conveniently packaged in plastic bags, ensuring their safety and intact transportation.
"Such clothes are preferred by locals because they look brand new, are packed in diverse sizes with labels, and the pakaging is transparent for a buyer to choose any colour of their choice.”
This, the source said, is not the case with Made-in-Rwanda clothes, because local manufacturers are prohibited from packaging in plastic bags.
According to the entrepreneur, challenges around packaging for Made-in-Rwanda clothes, which are distributed in boxes, makes them susceptible to getting dirty, wrinkled, stained, and giving the impression of being second-hand or of poor quality.
"This undermines the value of Made-in-Rwanda products in the eyes of the public," the source added.
"When some manufacturers and I inquired with the Rwanda Environment Management Authority (REMA) about why imports are allowed to be packaged in plastic bags, their response was that international standards authorise the use of plastic bags for packaging in order to ensure that the clothes are shipped in a good condition,” the manufacturer explained.
The entrepreneur called upon REMA to grant permission to local manufacturers to package in plastic bags, especially those in mass production.
"If 90 per cent of clothes are imported in plastic bags and they are regulated, I believe that the plastic bags used for the remaining 10 per cent (locally made clothes) can also be regulated.”
The entrepreneur noted that the packaging problem has seen Made-in-Rwandan manufacturers lose business deals.